Welding is a critical technique in modern fabrication, allowing for strong, reliable, and durable connections in various applications. A frequently asked question among professionals and DIY enthusiasts is whether you can weld a half coupling to a pipe. The answer is yes, and with the proper techniques, this method creates a secure and long-lasting joint. Understanding welding a half coupling to a pipe is essential for ensuring the integrity of plumbing and industrial piping systems.
What is a Half Coupling?
A half coupling is a versatile pipe fitting designed for connecting or branching pipes within a system. Unlike a full coupling, which features threading on both ends to join two pipes, a half coupling has threading on only one side. This makes it a popular choice for creating outlets or attaching accessories such as valves and gauges to existing piping systems.
Half couplings are typically made from carbon steel, stainless steel, or brass materials, each offering unique advantages. For instance, carbon steel half couplings are known for their strength and affordability, making them ideal for industrial applications. Stainless steel couplings are corrosion-resistant perfect for pipelines in chemical plants or food-grade systems. Brass, often used in plumbing, combines malleability and resistance to corrosion, making it a preferred choice for residential and commercial setups. These features make half couplings a staple in industries like plumbing, oil and gas, chemical processing, and HVAC systems.
Why Weld a Half Coupling to a Pipe?
Welding a half coupling to a pipe offers multiple benefits, making it superior to other joining methods, such as threading or adhesives. The process ensures a connection that is durable and capable of withstanding high pressure and extreme temperatures, which are common in industrial environments.
One significant advantage of welding is the strength it provides. A properly welded joint is much stronger and more reliable than threaded connections, especially for heavy-duty pipelines. Welding also ensures a seamless connection, reducing the risk of leaks in plumbing or industrial systems. This is particularly important for pipelines transporting high-pressure fluids or gases. Additionally, welding allows for precise customization, enabling you to position the coupling exactly where needed without compromising the pipe’s structural integrity.
Welding becomes the go-to solution in scenarios such as adding a branch, installing instrumentation, or repairing a damaged pipeline. Its ability to handle vibrations, corrosion, and fluctuating temperatures makes it indispensable for various applications, from residential plumbing to industrial piping systems.
Can You Weld a Half Coupling to a Pipe?
Yes, welding a half coupling to a pipe is possible and is common in the fabrication and construction industries. However, careful attention to detail is required to ensure that the weld is secure, leak-proof, and capable of withstanding the demands of its application. Factors such as the type of materials, the thickness of the pipe, and the welding method must be considered to achieve a successful and durable weld. Proper preparation and adherence to industry standards, like those outlined by the American Society of Mechanical Engineers (ASME), are crucial to the process.
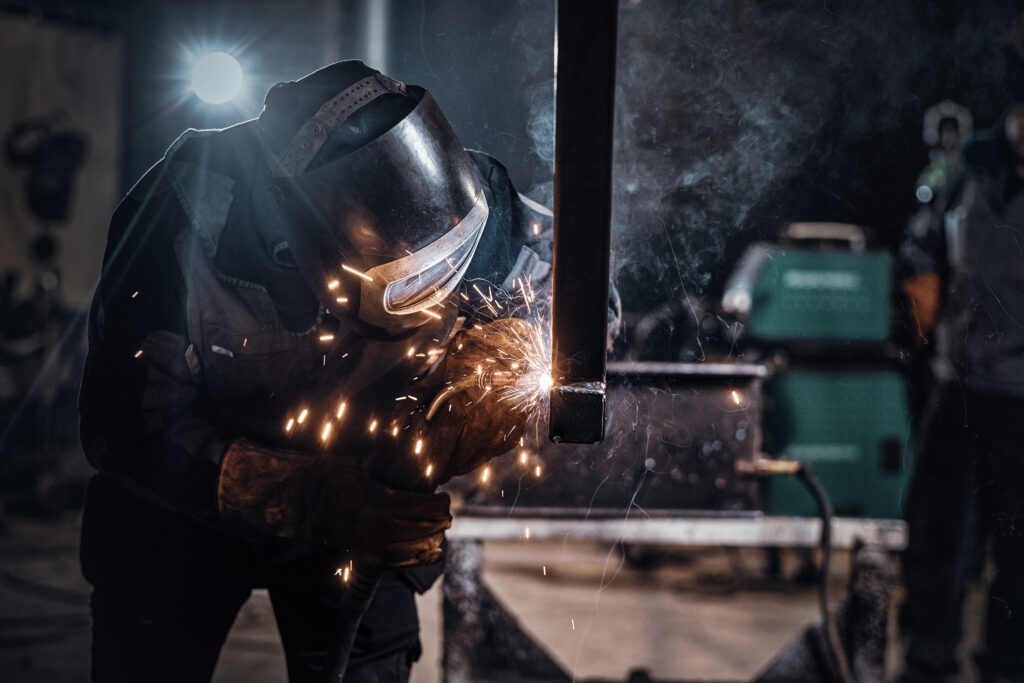
The Welding Process: Step-by-Step
1. Preparation
Preparation is crucial in welding a half coupling to a pipe, ensuring a clean and secure connection. Begin by thoroughly cleaning the pipe and the coupling to remove any debris, grease, rust, or paint that could compromise the weld. A clean surface creates a strong bond between the two materials. Use tools like a wire brush or grinder to achieve this.
After cleaning, align the half coupling with the pipe at the desired location. Proper alignment is critical, as any misplacement can lead to structural issues or leaks. Use clamps to secure the coupling and make tack welds to hold it during the final welding process. These steps set the foundation for a strong and accurate weld.
2. Material Compatibility
Ensuring material compatibility is key to a successful weld. The half coupling and the pipe must be made of materials that can be welded together without causing defects such as cracking or corrosion. For example, welding a carbon steel coupling to a stainless steel pipe requires unique filler materials to prevent issues like galvanic corrosion. Understanding the properties of the materials involved will help you choose the appropriate welding technique and filler material for your project.
3. Welding Method
Choosing the correct welding method is essential for achieving a strong and professional result. Three popular welding techniques are commonly used for this application:
TIG Welding (Tungsten Inert Gas): TIG welding is ideal for precision work, especially when dealing with thinner pipes or more delicate materials like stainless steel. It offers clean and controlled welds that are free from spatter.
MIG Welding (Metal Inert Gas): MIG welding is a faster option that is suitable for larger projects or thicker materials. It is user-friendly and provides a high level of control, making it ideal for fabricators of all skill levels.
Stick Welding: This versatile technique is commonly used for outdoor applications or heavy-duty pipelines. It works well in harsh environments and is compatible with various materials.
Each method has advantages, so selecting the one that best suits your materials and project requirements is vital.
4. Perform the Weld
Start by creating tack welds around the circumference of the coupling to secure it in place. This prevents movement during the welding process and ensures proper alignment. Once the coupling is stabilized, weld around the entire circumference using your chosen method. Consistent heat application and penetration are crucial for a strong and durable connection. Consider multiple welding passes for thicker pipes to ensure complete coverage and strength.
5. Inspection
After the weld is completed, inspect the joint for any defects, such as cracks, porosity, or incomplete fusion. These issues can weaken the joint and lead to leaks or structural failure over time. Non-destructive testing methods, like X-rays or ultrasonic testing, are recommended for critical applications, such as high-pressure pipelines or industrial systems.
6. Post-Weld Treatment
Once the weld is complete, clean the joint thoroughly to remove any slag or debris left behind. For outdoor or corrosive environments, applying a protective coating or paint can prevent rust and extend the lifespan of the connection. Proper post-weld treatment is essential for maintaining the integrity of the joint.
Tips for Successful Welding
Use the Right Equipment: Invest in high-quality welding equipment that matches the requirements of your materials and project. This ensures consistent performance and professional results.
Choose the Correct Filler Material: The filler material must be compatible with the pipe and the half coupling to prevent defects like cracking or corrosion.
Follow Industry Standards: Adhering to guidelines, such as those set by ASME for piping systems, ensures that your work meets safety and performance standards.
Practice Safety Measures: Welding involves high heat and electrical currents, so wearing protective gear and working in a well-ventilated area is essential for safety.
Applications of Welded Half Couplings
Welded half couplings are used in a variety of industries thanks to their strength and versatility:
Plumbing Systems: They create access points for valves, faucets, or hose connections in residential and commercial plumbing systems.
Industrial Piping: They are commonly used to add instrumentation, such as gauges or sensors, to high-pressure pipelines.
Oil and Gas Industry: Half couplings are indispensable for pipeline modifications and repairs that transport oil, gas, or other fluids.
HVAC Systems: They connect pipes for heating, cooling, and ventilation, ensuring leak-free performance.
Challenges and Solutions
Although welding a half coupling to a pipe is a straightforward process, challenges can arise:
Heat Distortion: Excessive heat during welding can warp the pipe or coupling. To avoid this, use controlled welding techniques and allow the materials to cool gradually.
Alignment Issues: Misaligned fittings can lead to stress and leaks in the pipeline. Using clamps and precise measurements can prevent this issue.
Material Incompatibility: Always verify material compatibility before welding. Using the wrong combination can result in defects or early failure of the joint.
Conclusion
Welding a half coupling to a pipe is a practical and efficient solution for creating secure and leak-proof connections in plumbing and industrial systems. You can ensure a strong and durable joint by following the proper preparation steps, selecting the right materials, and using appropriate welding methods.
If you’re looking for expert welding services in Orange County, Smith Welding & Fabrication specializes in high-quality pipe welding and custom fabrication projects. Contact us today to discuss your needs and get a free quote!