In metal fabrication, welding is a foundational process that combines raw materials to form the products, structures, and components we rely on daily. Whether working on a custom metal project or assembling large-scale structural frameworks, understanding the fundamentals of welding joints is essential. Perhaps you’ve asked: What are the 5 basic types of welding joints? In this guide, we’ll explain these five joint types in depth, describe their unique characteristics, discuss when and why they’re used, and explore the best welding processes to achieve strong, reliable connections.
By understanding these basic welding joint types—butt joints, corner joints, lap joints, tee joints, and edge joints—you’ll be better equipped to select the right approach for your next project. Along the way, we’ll cover essential considerations like joint preparation, welding techniques, and tips for achieving high-quality welds. Whether you’re a seasoned welder, a metal fabrication professional, or a curious DIY enthusiast, this comprehensive look at the core categories of welding joints will help you achieve better, more consistent results.
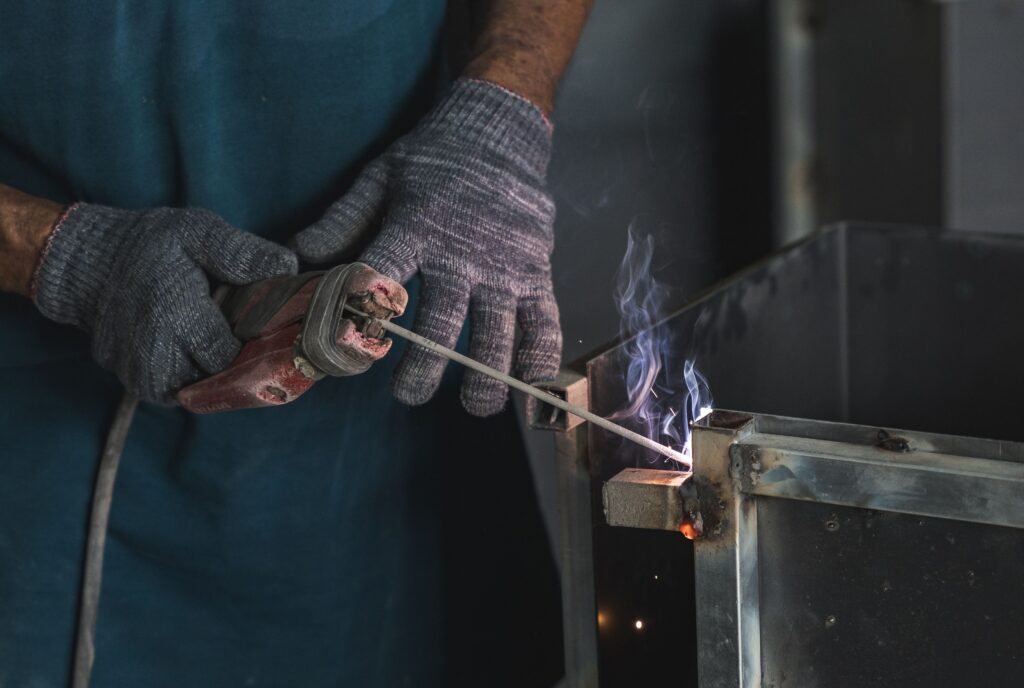
Why Understanding Welding Joints Matters
A welding joint is where two metal pieces are brought together for welding. The geometry of this connection influences the weld’s strength, ease of access, necessary welding procedures, and the final product’s durability. From the perspective of a fabrication shop or professional welder, knowing how and when to apply a specific welding joint type can:
- Optimize Material Usage: Selecting the appropriate joint type can minimize material waste and improve efficiency.
- Improve Structural Integrity: The right joint design contributes to the strength and longevity of a structure or component.
- Enhance Quality and Reliability: A proper joint helps ensure the weld meets functional and safety requirements.
- Streamline Production: Certain joints lend themselves more easily to automation, standardized procedures, and repeatability.
As you weigh the advantages of each type of weld joint, keep in mind the material thickness, joint configuration, welding position (flat, vertical, horizontal, overhead), and the chosen welding process, such as Shielded Metal Arc Welding (SMAW), Gas Metal Arc Welding (GMAW/MIG), Flux-Cored Arc Welding (FCAW), or Gas Tungsten Arc Welding (GTAW/TIG). Your familiarity with these methods and a solid understanding of welding joints will guide you toward the best possible outcome for any project.
1. Butt Joints
Definition: A butt joint is formed when two workpieces are placed on the same plane, with their edges meeting end-to-end. This is one of the most common and straightforward joint configurations. You’ll see butt joints in everything from pipeline construction to structural beams and sheet metal fabrication.
Key Characteristics:
- Ease of Preparation: Butt joints generally involve simple edge preparation. You might bevel the edges in thicker materials to achieve deeper penetration and stronger welds.
- Good Load Distribution: When done correctly, butt joints distribute loads evenly across the connected pieces.
- Versatility: Butt joints are compatible with multiple welding processes, including SMAW, GMAW, FCAW, and GTAW, as well as oxy-fuel welding in some cases.
When to Use Butt Joints:
Butt joints work best when you need a clean, continuous connection between two plates or pipes. They are ideal for pipelines, structural steel frameworks, and plate metal fabrication projects where alignment and a straight, uniform weld line are critical.
Tips for Successful Butt Joints:
- Edge Preparation: Bevel thick materials to achieve full penetration. The angle and depth of the slope will depend on the material thickness and the welding code requirements.
- Root Opening: Maintain a consistent root opening (the gap between the two joined pieces) to ensure proper weld penetration.
- Proper Welding Process: Choose a process that provides the desired penetration and weld finish. For example, GTAW (TIG) welding can give precise, high-quality welds on thinner materials, while GMAW (MIG) or SMAW might be better suited for heavier plates.
2. Corner Joints
Definition: A corner joint is formed when two metal pieces meet at a right angle, usually with one piece positioned on the edge of the other. The result typically resembles an “L” shape. Corner joints are common in fabricating frames, boxes, and other enclosed or partially enclosed structures.
Key Characteristics:
- Variety of Configurations: Corner joints can be “open” or “closed,” depending on how the plates are arranged. An open corner joint leaves a V-shaped gap, while a closed corner joint brings the edges flush against each other.
- Aesthetic Considerations: Corner joints must be strong and visually appealing in some decorative or structural projects.
- Versatility in Welding Processes: Like butt joints, corner joints can be welded using MIG, TIG, stick, or flux-cored welding methods.
When to Use Corner Joints: Corner joints come into play when fabricating boxes, frames, enclosures, and certain structural elements where a 90-degree connection is required. They’re also common in ornamental ironwork, furniture, and sheet metal constructions such as ductwork or cabinetry.
Tips for Successful Corner Joints:
- Fit-Up Matters: Ensure the pieces fit snugly without significant gaps. Better fit-up translates to a cleaner weld and improved joint strength.
- Consider Joint Design: Open-corner joints may require more filler metal, while closed-corner joints can reduce distortion and improve aesthetics.
- Use Proper Technique: Ensure adequate penetration into the corner’s root area, depending on your chosen process. With TIG welding, precise heat control can reduce warping and produce a smooth, attractive weld bead.
3. Lap Joints
Definition: A lap joint is formed when two pieces overlap, often with one piece extending over the other. It’s a typical joint in sheet metal fabrication and is widely used in the automotive and construction industries.
Key Characteristics:
- Ease of Alignment: Lap joints don’t require edges to meet perfectly, making them more forgiving for specific applications.
- Multiple Weld Bead Options: You can weld along one or both edges of the overlapping piece. Double-sided lap welds provide greater strength.
- Ideal for Thin Materials: Because lap joints don’t require beveling or complicated joint preparation, they’re excellent for joining thinner metals where full-penetration butt welds would be more difficult.
When to Use Lap Joints: Lap joints are commonly used when joining materials of differing thicknesses or when an extended tab of one piece is desirable for alignment and positioning. You’ll find them in automotive body panels, HVAC ducting, and structural components where complete edge-to-edge fitting is unnecessary.
Tips for Successful Lap Joints:
- Minimize Gaps: Even though lap joints are forgiving, strive for minimal gaps to ensure a strong weld and reduce the risk of corrosion or moisture entrapment.
- Avoid Excessive Overlap: Too much overlap may waste materials and add unnecessary weight. Keep overlaps strategic and functional.
- Use the Right Process: MIG or TIG welding can produce smooth, controlled welds on lap joints. For thicker materials, SMAW or FCAW might be better suited.
4. Tee Joints (T-Joints)
Definition: A tee joint is formed when one piece of metal is positioned perpendicular to another, creating a T-shaped intersection. This type of joint is often used to connect structural supports, cross-members, and components where load transfer is essential.
Key Characteristics:
- 90-Degree Intersection: The joined piece rests against the flat surface of the other, creating a T configuration.
- Strong Load-Bearing Capability: Tee joints often carry significant loads, primarily when properly welded and reinforced.
- Weld Accessibility: Typically, welders have good access to both sides of the joint, allowing for strong, multi-pass welds when needed.
When to Use Tee Joints: Tee joints are ubiquitous in structural applications, such as building frames, support braces, and trusses. They’re also found in machinery frames, heavy equipment fabrication, and industrial platforms where strength and rigidity are essential.
Tips for Successful Tee Joints:
- Proper Fit-Up: Ensure the plates align properly to avoid uneven weld beads and stress concentrations.
- Consider Weld Sequencing: Start welding in the center and move outward, or use balanced welding techniques to reduce distortion.
- Penetration is Key: Full penetration at the joint’s root ensures maximum strength and helps the weld withstand dynamic loads.
5. Edge Joints
Definition: An edge joint is formed when two metal pieces are placed side-by-side with their edges parallel and touching. They are often used in sheet metal work where a joint is needed at the edges of thin plates.
Key Characteristics:
- Limited Strength in Some Cases: Because the weld only fuses the edges, edge joints may not support heavy loads as effectively as butt or tee joints.
- Preparation and Cleaning: Proper edge preparation is essential. Edges must be clean and free of scale, rust, and other contaminants.
- Reduced Visibility of Welds: Sometimes used where aesthetics are not critical since the weld will be at a subtle edge intersection.
When to Use Edge Joints: Edge joints are common in lightweight structures, sheet metal enclosures, and minor reinforcements. They’re also used when sealing the edges of sheets or plates to prevent leaks, contamination, or sharp edges.
Tips for Successful Edge Joints:
- Thin Materials Only: Edge joints are best for thinner materials where penetration is more straightforward and complete strength is not required.
- Welding Technique: GTAW (TIG) welding offers fine control and can reduce the risk of burn-through on thin edges.
- Proper Filler Selection: Use a filler metal compatible with the parent material and the intended service environment.
Additional Considerations for Welding Joints
Knowing the five basic types of welding joints is only the beginning. To ensure your welds are strong, reliable, and meet professional standards, consider the following factors:
- Welding Process Selection:
Each welding joint may favor specific welding processes. For example, GTAW (TIG) offers precision and cleanliness, making it suitable for cosmetic welds or thin materials. GMAW (MIG) is faster and often preferred in production environments. SMAW (Stick) welding works well outdoors and in field conditions, while FCAW (Flux-Cored) can handle thicker materials and less ideal conditions. - Filler Metals and Consumables:
The choice of filler metal, shielding gas, or flux dramatically influences weld quality. Matching the filler metal to the base metal and desired mechanical properties ensures consistent, high-strength welds. For example, stainless steel projects require stainless steel filler rods, while carbon steel requires carbon steel filler materials. - Joint Preparation:
Proper preparation is crucial. This includes cleaning off rust, mill scale, paint, oil, or grease. Beveling or grinding edges to a specific angle encourages better penetration and stronger welds. Neglecting preparation can lead to weld defects like porosity, incomplete fusion, or cracking. - Welding Position and Accessibility:
Welding in the flat position is generally the most manageable and provides the best results. However, real-world conditions often require overhead, vertical, or horizontal welding. Certain joint types are more straightforward to weld in certain positions. For instance, butt joints on flat surfaces are more straightforward to handle than corner joints overhead. - Heat Input and Distortion Control:
The metal expands and contracts as it’s heated and cooled. Managing heat input, using proper welding sequences, and employing techniques like backstepping can reduce distortion and residual stresses. The best welders understand how to balance heat and travel speed to minimize warping while achieving the desired weld penetration. - Inspection and Quality Assurance:
After welding, inspections using visual examination, dye penetrant testing, ultrasonic testing, or X-ray testing may be required—especially in critical industries like aerospace, pressure vessel fabrication, or structural construction. Ensuring each joint meets set standards and passes inspections is vital for long-term reliability and safety.
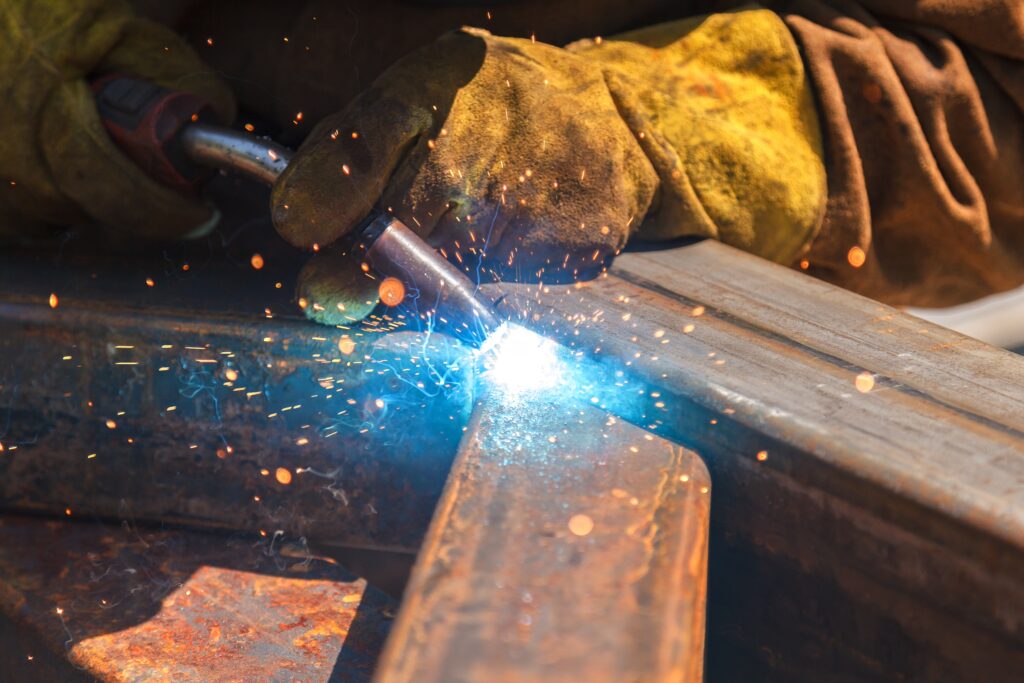
Applying This Knowledge in Professional Settings
Understanding these welding joints is more than theoretical for Smith Welding & Fabrication fabrication professionals and similar operations. It informs daily decision-making, from approaching a new project’s design to selecting the right welding personnel, procedures, and quality controls.
- Optimizing Fabrication: By identifying the correct joint configuration from the start, metalworkers can save time and materials, streamline production, and produce consistently high-quality results.
- Meeting Industry Standards: Many industries have strict guidelines (e.g., AWS D1.1 for structural steel). Understanding these joint types helps ensure compliance with relevant codes and standards.
- Enhancing Customer Satisfaction: Delivering products with reliable, visually appealing welds that stand the test of time leads to happier clients and stronger business relationships.
Speak With Our Team Today
If you’ve ever asked, What are the 5 basic types of welding joints? Now you have a comprehensive answer: butt joints, corner joints, lap joints, tee joints, and edge joints. Each type serves a distinct purpose, offering advantages, challenges, and best-use scenarios. By understanding when and how to apply these joint configurations, you can elevate your welding projects—improving your fabricated products’ efficiency, quality, and overall performance.
Don’t forget that choosing the right welding process, performing proper joint preparation, and carefully managing heat input and welding technique are all integral components of creating strong, durable welds. At Smith Welding & Fabrication, we pride ourselves on leveraging industry knowledge, best practices, and top-quality welding techniques to ensure that every project we undertake meets the highest structural integrity and craftsmanship standards.
From basic box frames to complex industrial assemblies, the core principles of these five welding joints guide us to produce exceptional results. Remember these fundamental joint types as you explore welding techniques and metal fabrication processes. They are the building blocks upon which the entire art and science of welding are built.