The US Bureau of Labor Statistics reveals about 428,000 people are working as welders, cutters, solderers, and brazers, with jobs expected to increase by 2% from 2021 to 2030. Welding fabricators work in diverse industries and use specialized equipment to cut, join and shape metal and other materials. They also make components and parts for different applications, including engines, machines, electrical equipment, toys, and household appliances. This skilled personnel can create sets of components or work on individual pieces. This blog provides an overview of welder fabricator careers, including their education, experience, and skills.
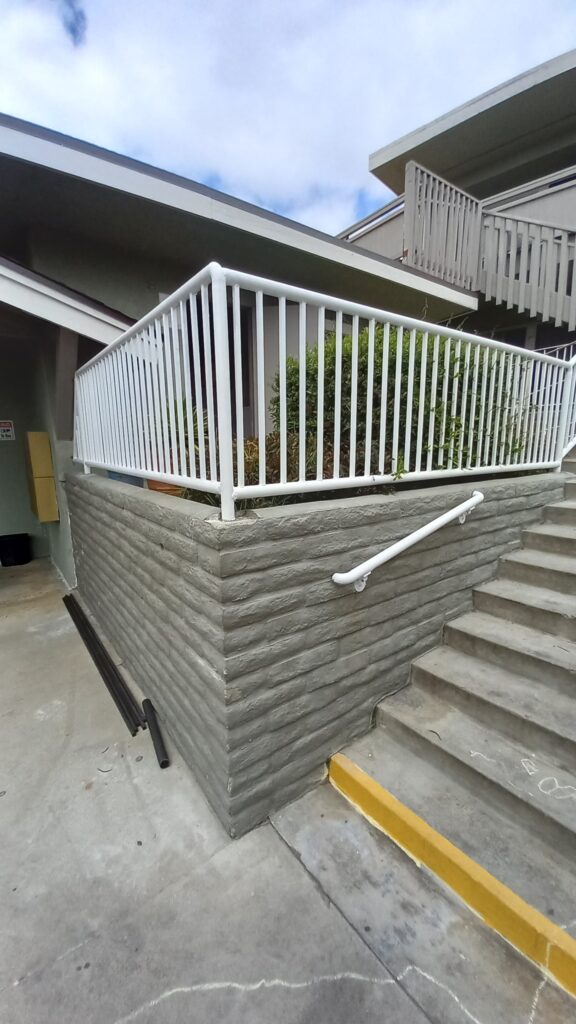
What is a Welder Fabricator?
A welder fabricator is a skilled person who uses welding and fabrication techniques to fabricate various products in manufacturing shops. They cut, machine, weld, and shape metal parts used for various metal and steel structures and create product components. Their roles include reading blueprints or technical drawings to determine the best techniques to cut the metal and fabricate the required item. Welding fabricators collaborate with designers and engineers to select raw materials and create ideal designs for a specific project or application.
Welder Fabricator Duties and Responsibilities
Welder fabricators construct and manufacture metal parts and products while taking particular care to produce clean, polished welds. They are required to follow blueprints, determine material measurements, and fabricate parts used in the later assembly process. They are also required to perform various tests to ensure weld quality and tolerance. Specific responsibilities include:
- Consulting and reading blueprints, drawings, and schematics to produce products to the required specifications
- Cutting, shaping, and welding parts as per the blueprint
- Machining fabrication materials and components
- Fitting, setting, and installing fabricated structures
- The steps to becoming a welder fabricator
- Metal forming, bending, and finishing
- Repair, design, layout, and estimation
- Supervise shop hands and helpers.
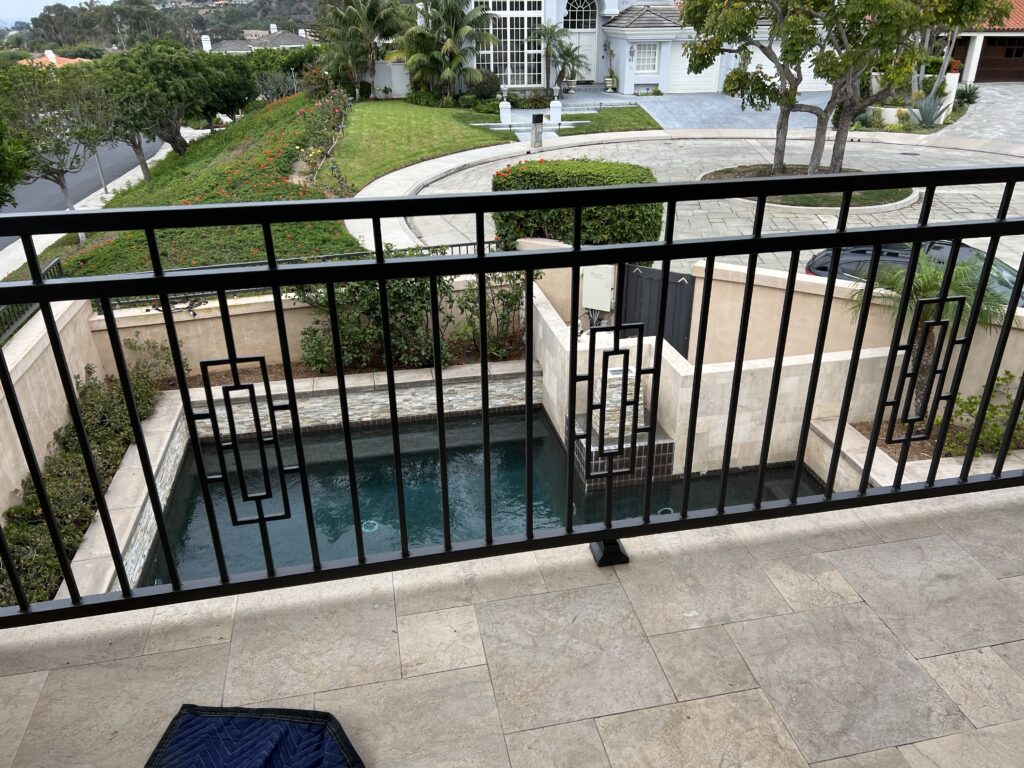
Education and Skills Of A Welder Fabricator
Many people interested in welding careers receive training from a trade school. These schools equip students with various skills related to welding and fabrication, including laser welding, underwater welding, and automated welding. Students also learn ultrasonic welding, gas metal arc welding, pipe welding, plasma welding, pipe fitting, and blueprint reading. Beginning classes usually last up to one year, but those looking for specific training should expect classes to last longer. Many trade schools offer students an opportunity to receive certification from the American Welding Society after the training.
Key Steps to Become a Welder Fabricator
The following is a summary of the steps to become a welder fabricator:
- Step 1: prepare in high school: The American Welding Society advises one should strive for a well-rounded education in high school. One should take shop, math, and science courses in addition to welding if the school offers them.
- Step 2: undergo training: Although one can get welding and fabrication skills on the job, most employers prefer applicants with some formal instructions. Training is available in vocational and technical schools, trade schools, community colleges, private academies, and the military. These schools offer certificate programs in specific welding and fabrication techniques, such as blueprint reading, drafting, metallurgy, and site safety.
- Step 3: consider certification: The next step is to get a certification from the American Welding Society’s Certified Welder (CW). The CW exam tests one’s ability to perform welding procedures used with sheet metal, petroleum pipelines, chemical refineries, and structural steel. To remain certified, one must submit a maintenance form every six months to verify their continued employment as a welder fabricator.
Work experience
Work experience is crucial to gaining employment within the construction and manufacturing industries. Potential employers expect to see work experience listed on their CV. After the training and certification process, candidates should gain experience by working as an apprentice in a company offering welding fabrication services.
Skills
Apart from education and experience, one should also have the requisite skills to become a successful welder fabricator. Core skills that employers often look for include:
- Ability to use a variety of tools and equipment
- Attention to detail
- Engineering and technology exposure
- Basic math and design skills
- Problem-solving skills
- Blueprint reading skills
- Critical thinking skills
- Knowledge of industry safety practices
Tips for Finding the Best Welder Fabricator
Before one hires a welder fabricator, there are several factors to keep in mind which help vet the skills and reputation of the candidates. The following are some simple tips for choosing the right welder fabricator for a custom fabrication project or repair:
- Qualifications: A welder should provide copies of the licenses and certification cards issued by AWS. The AWS certification verification page search should return the welder’s name, license or certification number, and expiration date. Depending on the type of project and industry, candidates may also be required to provide industry-specific welder certifications from the American Petroleum Institute and the American Society of Mechanical Engineers.
- Knowledge and experience: skilled welder fabricators should be skilled, knowledgeable, and experienced in their trade. They should be up to date on the latest fabricator techniques and building codes. Owing to their vast knowledge and years of practice working with different metals, experienced welder helps speed up projects by completing them within the estimated time frame without sacrificing quality.
- Insurance: Working with metal, heat, sharp objects, and heavy tools poses potential accidents. The right welder fabricator should be insured to protect an employer from financial consequences related to claims, including bodily injury, third-party property damage, and personal injury.
Smith Welding & Fabrication Provides Exceptional Solutions
Welder fabricators play a critical role in completed projects of various sizes, including machinery, bridges to bicycles, and common household appliances. Their job involves reading blueprints and designing, cutting, and shaping metal to create specific shapes and products.
Smith Welding & Fabrication is a leading welding company specializing in fencing and gates. We work on any metalwork and materials, including steel, wrought iron, aluminum, and stainless steel. Our licensed, bonded, and insured welder fabricators have provided customers with exceptional service experiences for 10+ years. No job is too big or too small. Contact us to schedule a free consultation.